Solutions for Oil-and-Gas Industry
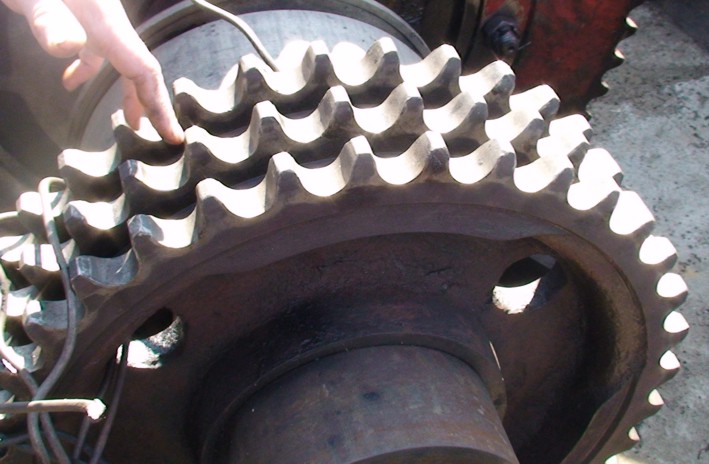
As the results of monitoring show, the
Specialists of STC ELECTRORESURS have developed technological solutions which solve these problems by means of the following operations:
- hardening — laser hardening of separate parts of the equipment and thread of pipes exposed to the greatest wear during operation to considerably increase their service life; this technology helps to avoid through embrittlement of parts unlike other HFC technologies.
- We possess the hardening technology and experience in laser hardening of diamond tools, such as diamond bits, diamond wheels and diamond reamers, increasing efficiency of tools by 30, 100 and 500%, respectively.
- laser alloying allows to harden parts made of unhardened cheap steels to the level of alloyed instrument steels. Various compounds are available for
abrasion-resistant surfaces. As compared with HFC hardening, the abrasive resistance increases 3,2 times. Low cost of the process makes it attractive for wide implementation. - cleaning by pulse laser allows to remove active substances destructing metal surface from micro cracks in the equipment (and to clean the equipment in whole). As a result of laser treatment the surface acquires anticorrosion properties.
-
build-up welding for recovery ofthin-walled equipment components worn out during operation. Metal powder is built up on damaged surface locally with high precision to considerably save the funds for equipment replacement and alloying materials; reduced consumption of filler materials also contributes to economy cut. -
build-up welding ofabrasion-resistant materials including nonmetallic hard andsuper-hard components with volume ratio of up to 75–85%. Tests ofbuilt-up surfaces in abrasive medium and by friction against a solid have demonstrated improvement of equipment durability 6 times - We have developed the technology and filler materials for frictional tools,
thread-cutting dies, drilling rig cams and wrenches that do not require flats. We also have developments on hardening of drilling rig brake disks with operation life improvement 2 times and increase of braking speed and equipment efficiency. -
high-precision cutting and welding of metals of different strength and thickness are especially effective during manufacture of pipes for sorting the raw material from big admixtures and slotted filters for sifting sand andsmall-sized admixtures. Use of fiber laser withvario-head allows to perform these operations at high speed and accuracy. For example, in slotted filters the slots have very small size (0.1 — 0.2 mm) and different direction — such operation can be performed only by application of the technology developed by us. The processes of orbital welding of pipes and welding of end pieces without filler materials and without deformation are being effectively tried out as well.
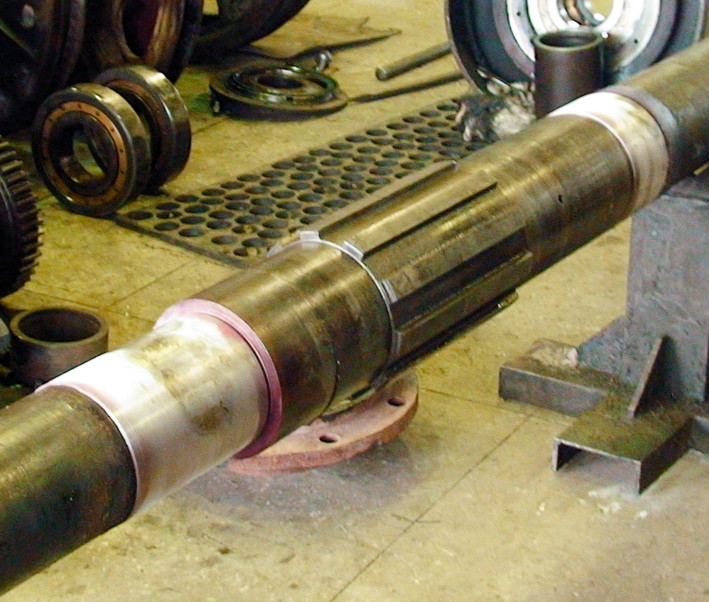
It shall be noted that application of integrated electric drives with high positioning accuracy in laser machines affect the accuracy of operations. Our company has also developed such electric drives. Versatility of
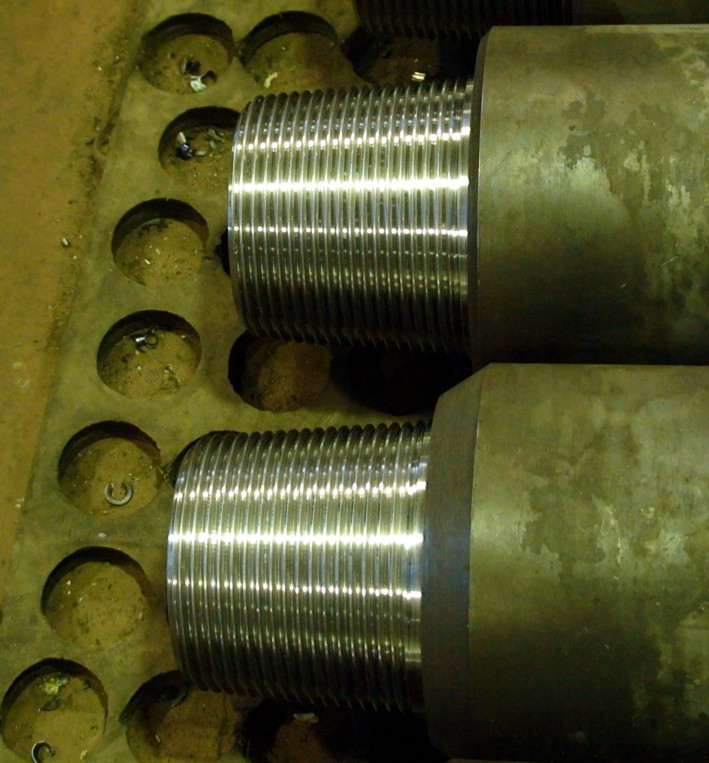
In the long term it will be possible to consider fibre laser application specific to